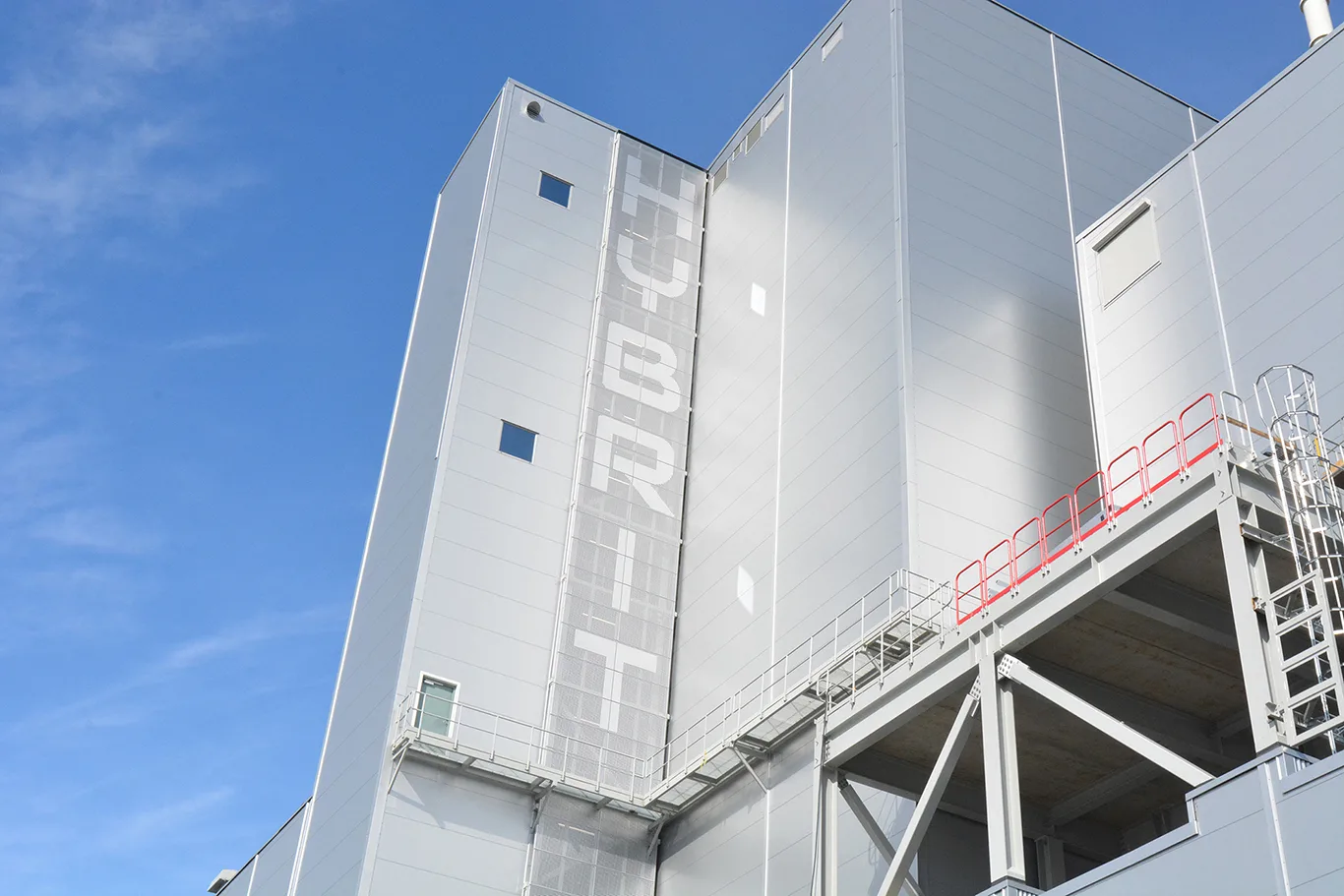
Future supplier of carbon dioxide-free sponge iron
Central to our transformation is the gradual shift to carbon dioxide-free sponge iron (HBI). We'll use hydrogen produced from fossil-free electricity in the reduction process, instead of coal and coke. The byproduct? Just plain water, not carbon dioxide.
Joining forces with our HYBRIT project partners SSAB and Vattenfall, our goal is to develop a fossil-free value chain for iron and steel production, potentially cutting Sweden’s carbon dioxide emissions by as much as ten percent.
This transformation is a journey: we’ll progressively scale up sponge iron production using innovative, circular technology. This way we’ll strengthen our position in the value chain and increase the value of our products by selling more refined iron, while enabling significantly reduced carbon dioxide emissions throughout the entire value chain. In the meantime, we’ll remain a dependable supplier of pellets and other iron ore products.