LKAB is charging up for battery-powered machinery under ground
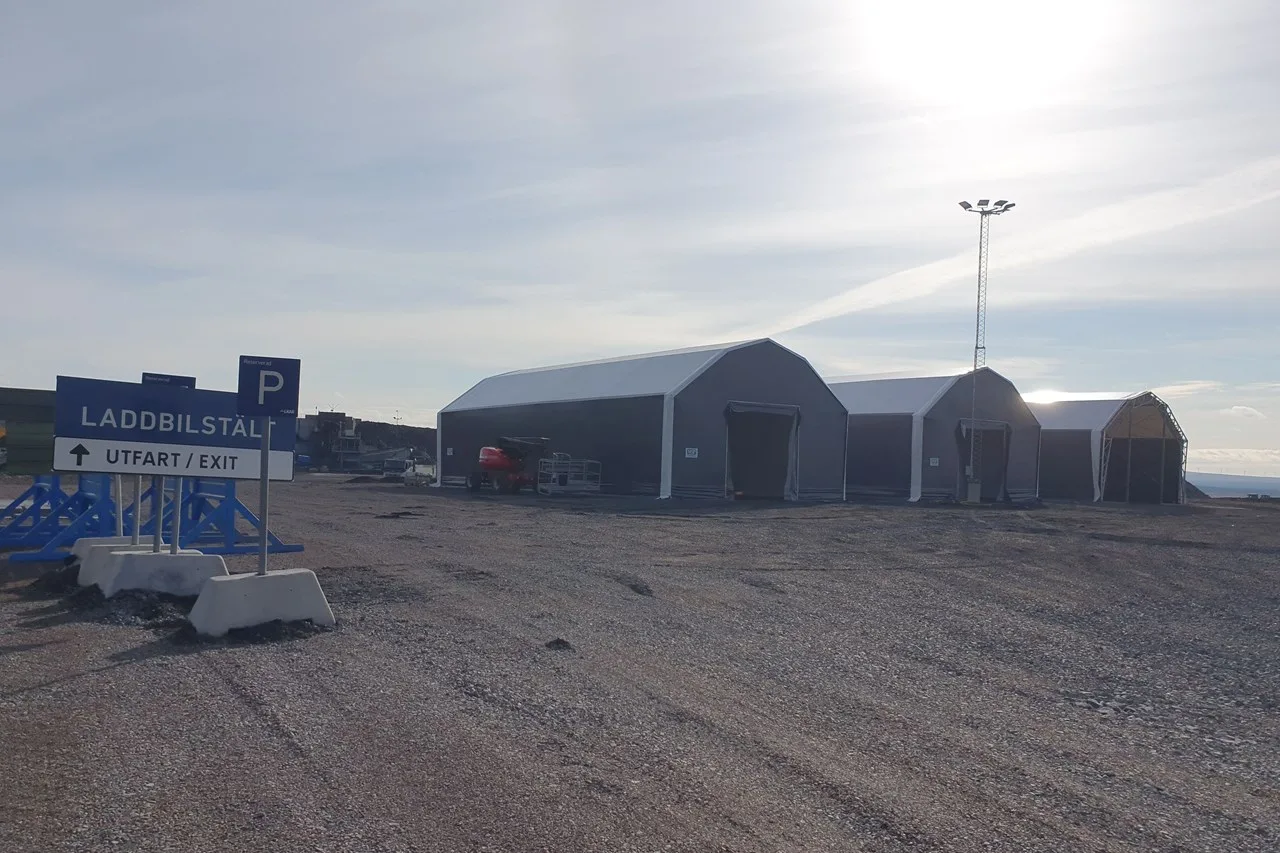
We're taking the next step towards a carbon-dioxide-free mine. Battery-powered machinery from Epiroc will be tested in conjunction with the innovation project which LKAB is running in collaboration with ABB, Combitech, Epiroc and Sandvik, aimed at setting a new world standard for sustainable mining.
“We are working concurrently along several tracks in all of our operations to eventually phase out diesel engines. We are testing the capacity of battery-powered and electric vehicles and determining how remote-control equipment performs as compared to manually operated machinery. But the tests must not jeopardize current and future deliveries to our steel-industry customers. The decisions we take with respect to the choice of equipment must not only contribute to higher productivity but, above all, also a more sustainable mine and a safer work environment,” says Anita Oraha Wardi, project manager for autonomous, smart and carbon-dioxide-free machinery at LKAB.
There are many advantages with battery-powered machinery. Zero carbon-dioxide emissions benefit the climate, improve air quality in the mine and support LKAB’s ambition to realize carbon-dioxide-free processes and products. In addition, battery-powered vehicles are quieter. Oil consumption will also be reduced, since we will eliminate diesel engines, which require both fuel and regular oil changes.
New infrastructure is needed
But battery-powered vehicles also place entirely new demands on underground infrastructure. Among other things, in the Konsuln test mine in Kiruna, construction manager Joakim Stålnacke and his colleagues have made space for charging stations and prepared areas where a crane can change batteries on vehicles.
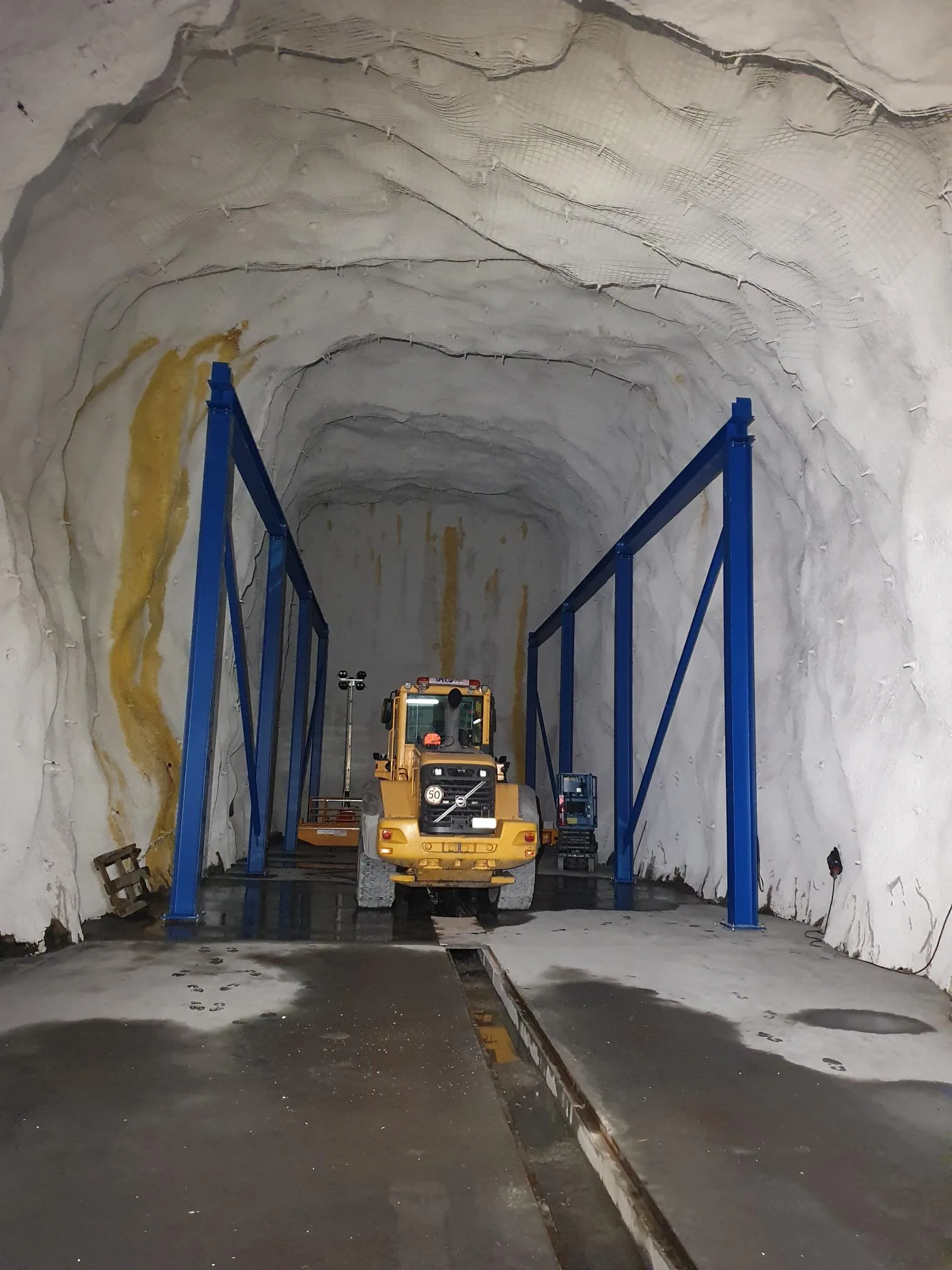
The machines must first be operated above ground. Together with Joakim Stålnacke, development engineer Atif Waheed and test manager Karl-Fredrik Abel have prepared a testing area close to the entrance to the test mine, in the southern part of LKAB’s industrial site. Here, consideration has been given to the test specifications produced by Atif Waheed. During the coming tests the infrastructure will both provide support and pose challenges.
Tests above ground
“We need to learn how battery-powered vehicles perform, and we can best do this by conducting structured tests above ground. Safety aspects have the highest priority and many issues have to be resolved before we roll down into the Konsuln test mine. We will share all of our findings with colleagues in Malmberget, Kiruna and Svappavaara, but also provide feedback to our collaborating partner Epiroc,” says Karl-Fredrik Abel.
“For us, this is the first time that Epiroc has had a battery truck underground in Sweden. Everyone involved from Epiroc in Örebro and from the Swedish sales company has learned an incredible amount over the past few months. There is a good cooperation between Epiroc, LKAB and Combitech and everyone is very positive about this battery transition. We look forward to having all three battery machines underground at LKAB and seeing them start to ‘work’ for real. Now we are taking a very big step forward for the whole mining industry and everyone involved can be very proud of that! says Morgan Rody, Senior Project Manager for autonomous, smart and carbon-free machines at Epiroc.
FACTS:An Epiroc Minetruck MT42-Battery with a payload of 42 tonnes will be delivered during autumn 2021. During the first quarter of 2022 an additional Minetruck MT42-Battery and a Scooptram ST14-Battery loader with a 14-tonne payload will be delivered. All vehicles will be tested at LKAB in Kiruna.
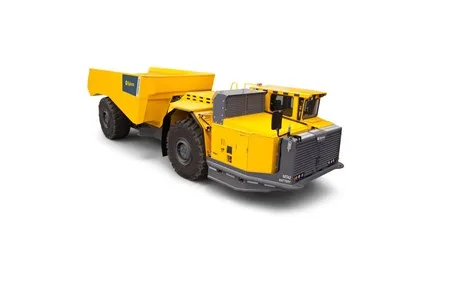