Increased sublevel height and new layout in LKAB’s Kiruna test mine
The deeper LKAB mines for iron ore, the higher the rock stresses it encounters. There are also increased distances for both development and the transport of ore, machinery and people, and therefore increased costs. In order to maintain LKAB's competitiveness and to ensure the continuation of safe mining, it was decided to test increased sublevel heights and a new type of layout – all within the framework of Sustainable Underground Mining (SUM).
Konsuln is located in the southern part of Kiirunavaara and is a small. almost separate, section of the Kiruna mine. Konsuln currently produces approximately 0.8 million tonnes of iron ore annually. as well as functioning as a test zone for the SUM project.One of SUM’s subprojects is DP1, which deals with mine layout and technology. The fundamental question that needs to be resolved is how LKAB will mine ore at depths of 2,000 metres or greater. Increased sublevel height and the fork layout may be part of the answer.
Development prepares for mining
In order to mine ore underground, transport routes must first be constructed – tunnels through the rock commonly known as drifts. This process is called development and involves the preparation of the area for mining.”We know that rock stresses increase with depth. In order to be able to continue working safely, we need to move our infrastructure further from the mining area, which increases development costs. If we increase the sublevel height from the current 29 to 50 metres then we will reduce the number of metres we develop and thereby reduce costs,” says Carlos Quinteiro, mining engineering specialist at LKAB and project manager of DP1 within SUM.By summer 2019, development will be completed on the 436-metre level at Konsuln. In parallel with this, work is ongoing at the next level, at a depth of 486 metres. A further level, at 536 metres, should be ready by the end of 2020.
New layout increases production capacity
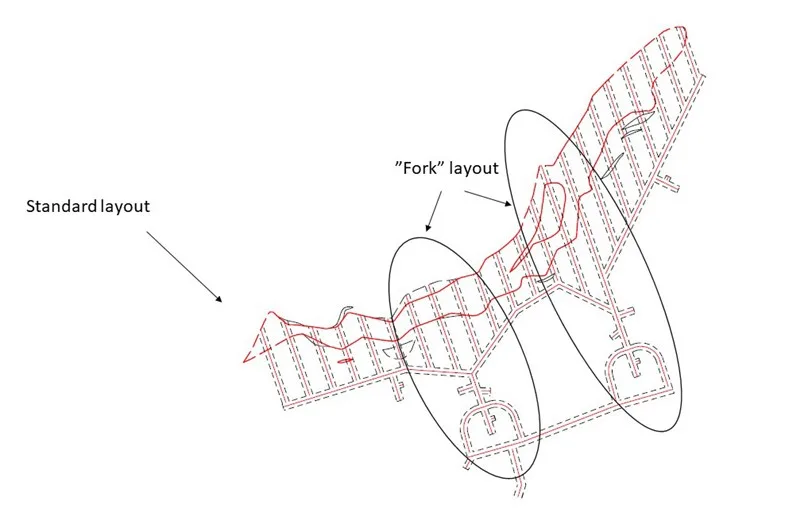
Parts of new levels at Konsuln will be designed with what is known as a fork layout. Among other things, this type of layout makes it possible to increase the total number of vehicles transporting ore from a production area, something that increases production capacity.”A fork layout allows the mine’s infrastructure to be moved further from the mining area, making it less susceptible to rock stress. We believe that this will improve stability; for example, in the rock excavation,” says Carlos Quinteiro.
A variety of vehicles, techniques and working methods will be tested at Konsuln. As early as August, testing will begin on what is for LKAB a new type of rig for drilling opening holes, the Easer from Epiroc. When LKAB Wassara has completed development of its coil-tube technique, water powered precision drilling technology for long and curved boreholes, this will also be tested and evaluated at Konsuln. LKAB Wassara and LKAB Kimit are also looking at improvements to charging technology for long boreholes. Another SUM subproject is preparing the way for autonomous electric vehicles by looking at how these will work alongside manually operated vehicles. A fully functioning collaboration with all of the various stakeholders is vital to progress.
Testing at Konsuln provides the basis for future mining
All test data from SUM should be collected by 2023, after which it will be used as a basis for decisions on future production systems at greater depths. The timetable is tight but Carlos Quinteiro is optimistic.
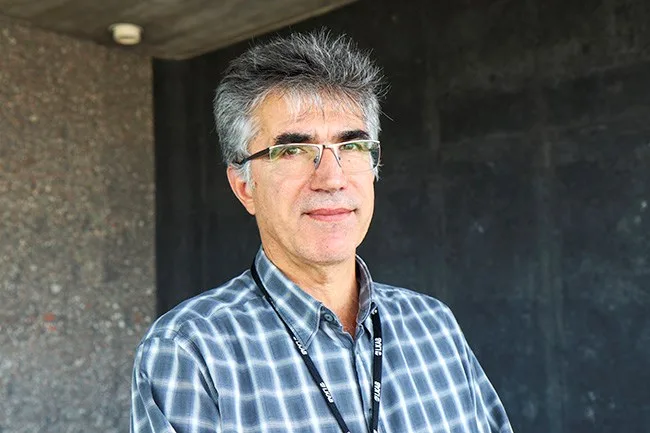
“LKAB has a long tradition of innovation and dedicated employees so I am convinced that we can meet these challenges. It is of course a matter of our competitiveness and, in the long term, LKAB’s survival,” says Carlos Quinteiro.