Collaboration for technological advance in Swedish steelmaking
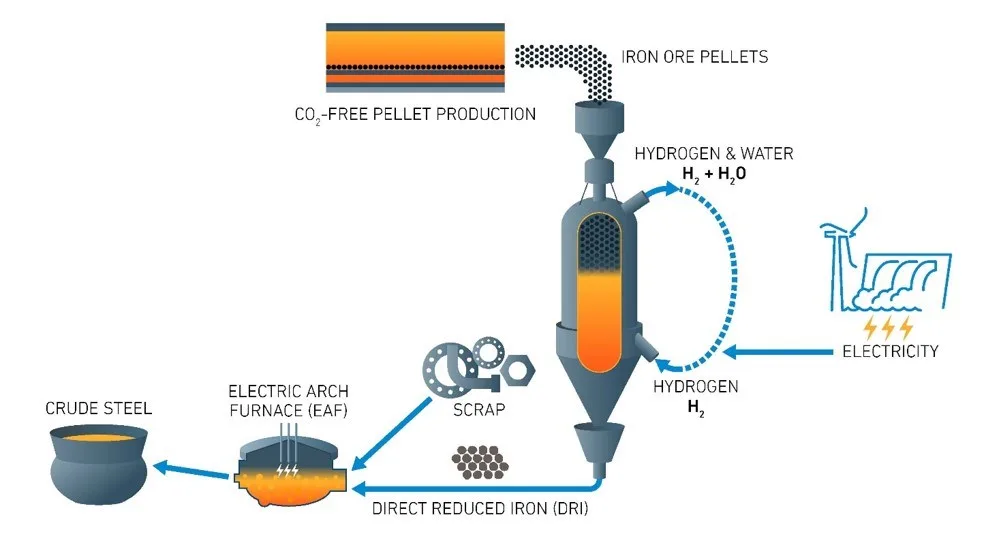
Construction of a world-unique pilot facility for fossil-free steelmaking has commenced. In the pilot plant a new process for direct reduction ironmaking will be tested. Here, hydrogen will be used instead of natural gas."It is always best to test a major process modification in small scale," says Magnus Tottie, research specialist at LKAB.
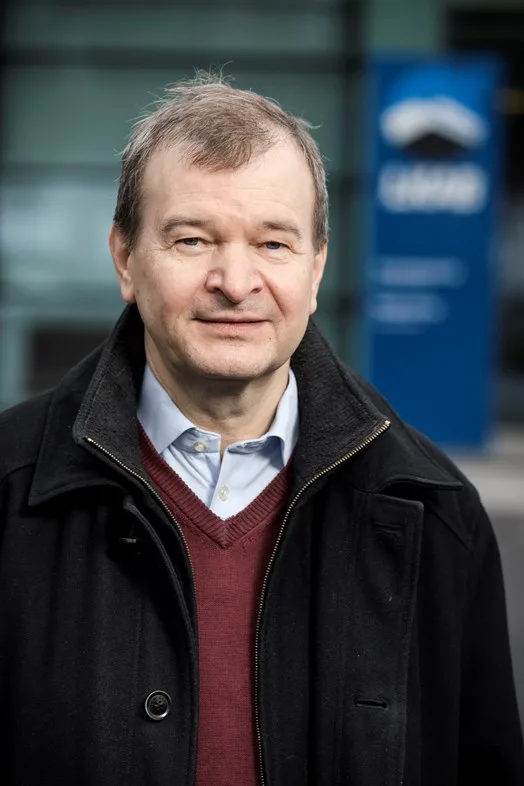
LKAB, SSAB and Vattenfall have formed a joint venture called HYBRIT Development AB and will apply specialist knowledge in their respective areas to develop a future method of steelmaking. The initiative can potentially reduce Sweden’s total carbon dioxide emissions by ten per cent and Finland’s by seven per cent. It has been described as decisive for Sweden’s ability to meet the targets set out in the Paris Agreement. LKAB is responsible for several stages of the HYBRIT programme, which is an important driver for the company.”We develop our own pellet process, as well as the direct reduction process, since we have learned a lot over the 50 years during which we have sold pellets to customers who make direct reduction iron. When it comes to pilot studies, we have gained a lot of experience from discussions with customers and we have a well-tuned organisation, since we have operated an experimental blast furnace in Luleå for the past 20 years. There, studies on ways of reducing CO2 emissions have also been done over the years,” says Magnus Tottie.
Magnetite provides advantages
LKAB’s iron ore consists largely of magnetite, which provides a great environmental advantage over competitors. Steel produced from 100 per cent LKAB pellets results in 14 per cent lower CO2 emissions compared to steel made in an average European sinter-based steel plant. One explanation is that it requires less energy to make pellets from magnetite than from hematite. The pellet process currently requires a lot of energy, while a very great amount of heat is released when magnetite is converted to hematite. One objective is to rely on magnetite heat.”Our vision is to reduce total fuel consumption in the pelletising plant as much as possible and to be not only fossil-free but also completely CO2-free. We are now working on studies with biofuel, electric heating and oxygen injection during heating,” explains Magnus Tottie.
System-wide challenges
LKAB emits about 700 kilotonnes of CO2 per year and SSAB emits more than five million tonnes. Today, coal and coke are used to reduce iron ore to iron. One of the ideas behind HYBRIT is to use hydrogen that has been produced from Swedish fossil-free sources instead. The residual product is water.”Actually, the greatest challenges are system-wide; to make the entire process chain work. Here, the ultimate problem that must be addressed is the role of carbon. A certain amount of carbon is needed in the final product; but how much carbon is enough? Another question is how to add it in the most effective way,” adds Magnus Tottie.
The HYBRIT programme focusses on the best solutions, business-wise, for LKAB, SSAB and Vattenfall.”The process will work with our old product. When the process functions, we’ll see if it is necessary to modify the product,” explains Magnus Tottie.
HYBRIT owns the technology, which is developed on the basis of a solid and growing reserve of knowledge and experience. The company will work to disseminate knowledge throughout the world with the hope of reducing CO2 emissions globally.”The prerequisites for success are good in Sweden, since we have fossil-free electricity, high-grade iron ore and a steel company with niche products,” says Magnus Tottie.
HYBRIT is divided into three phases:
- A prestudy to review all prerequisites, 2016–2017
- Pilot-scale trials, 2018–2024
- Trials in a demonstration facility, 2025-2035
Pilot study phase
Pilot studies of direct reduction of iron ore pellets with hydrogen and subsequent smelting in the electric arc furnace for steelmaking. The aim of the studies is to develop a concept whereby pure hydrogen is used as the reducing agent in the production of direct reduction iron from iron ore pellets. That is the core of HYBRIT and the phase that demands the most research and development.Pilot studies of fossil-free pellet heating cover fossil-free heating technology for sintering of iron ore pellets. The studies are aimed at reducing emissions from existing pelletising plants, as well as at developing a new pelletising process.