One of Sweden’s biggest industrial investments completed
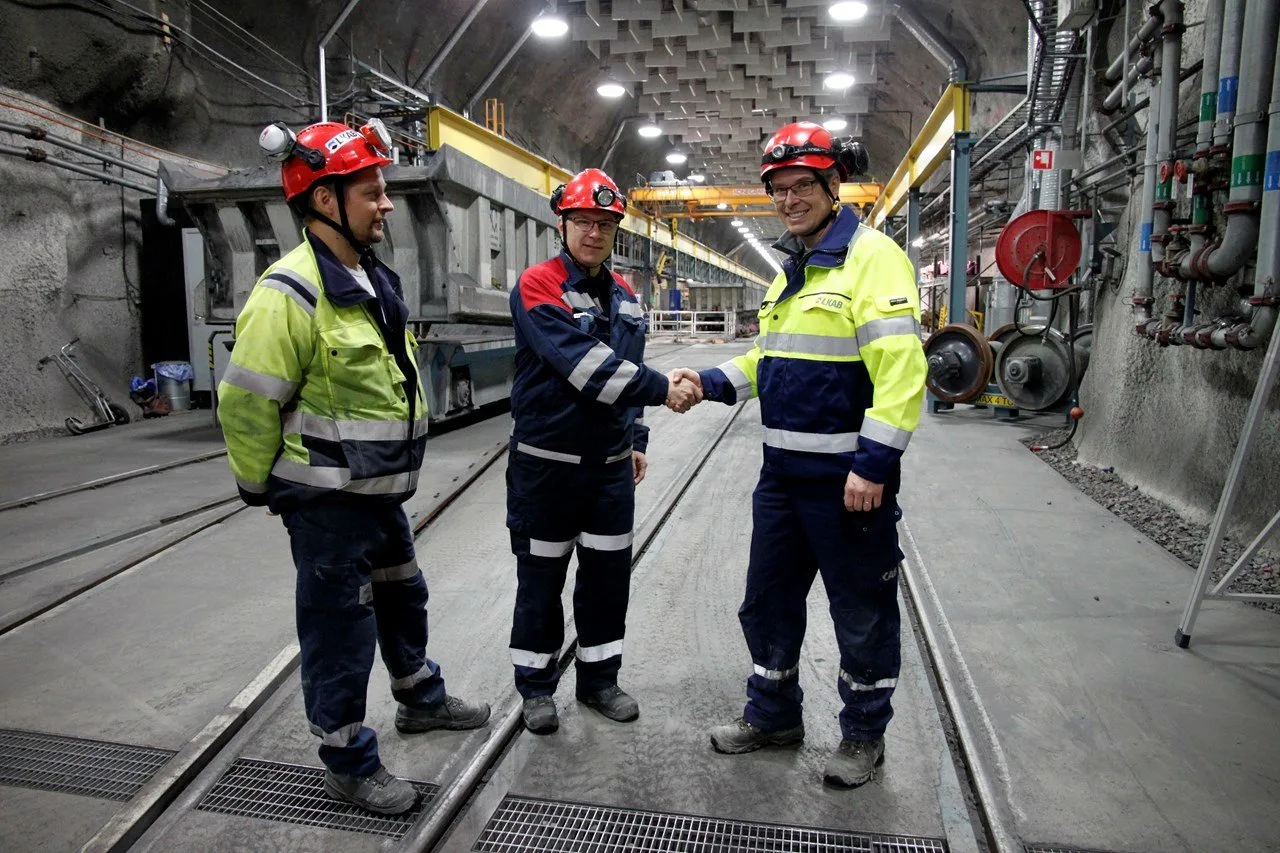
Nearly 4.3 million cubic metres of rock, the equivalent of seven Globe Arenas, has been excavated to make room for KUJ 1365. Now, about ten years later, LKAB's largest-ever single investment has been realized. The Kiruna mine's main haulage level, the seventh, is thereby complete.
On October 28th 2008 the board of LKAB announced the decision that a new main level would be built 1365 metres underground in the Kiruna mine. This signalled the start of an enormous project, one of LKAB’s largest ever. More than 1000 people from some 100 companies worked on the first stage, which was inaugurated with great ceremony in May 2013. Since then, five stages have been built at intervals of about one year.”We have built a large-scale facility that is designed to produce 35 million tonnes. Production-wise, we’re not quite ready yet, but things have settled down a bit, now that all five skip hoisting systems have been delivered and we can focus on production. This level will keep us busy until 2033, depending on how much we mine out,” says Lennart Stålnacke, manager, underground haulage systems.
The first stage consists of three shaft groups, each with four ore passes, two train sets, a crusher and a skip hoist, as well as power, water, ventilation and automation to run the level.The other four stages have largely involved other production apparatus, shaft groups, trains, crushers and skip hoists – all at a cost of about 12 billion kronor. The final stage was handed over for operation in November.”Work on the B12 hoist system and a shaft for trucks concluded this top-of-the-line project,” says Kari Oja, project manager.Despite the size of the project, all agree that everything has gone according to plan over the years. “We haven’t made any real design and dimensioning errors or been off-target with the overall design. One advantage of such a large and extensive project is that we have been able to eliminate systematic errors throughout the process. Of course, there are always bound to be hiccups along the way, but we have the situation under control. We will continue going through our checklist and working with optimization,” says Thomas Nordström, project manager.
What is your best memory from the project?”That was probably when we began work on the first stage. There were people everywhere, all building at the same time. We had coordination meetings every three hours,” says Kari Oja.A lot certainly has happened since then.In the final phase of the project about 30 to 40 people were working to complete the B12 skip hoist.”I think the inauguration is a very special moment, when everything is at its best, “says Thomas Nordström.The project group handed KUJ 1365 over to LKAB in December.”For me, the best feeling is when the whole level has been commissioned and is up and running. We have experienced some frustrating moments throughout the project, while at the same time there have been high demands on production. Now we’re seeing the start-up of a highly efficient production facility that will be utilized to full capacity,” says Lennart Stålnacke.At the same time, we must look ahead. LKAB is looking at future production facilities and presenting various proposals. But one major target has just been reached. The creation of a safe, modern and cost-effective main level and supporting infrastructure.