Reinforcement for the climate
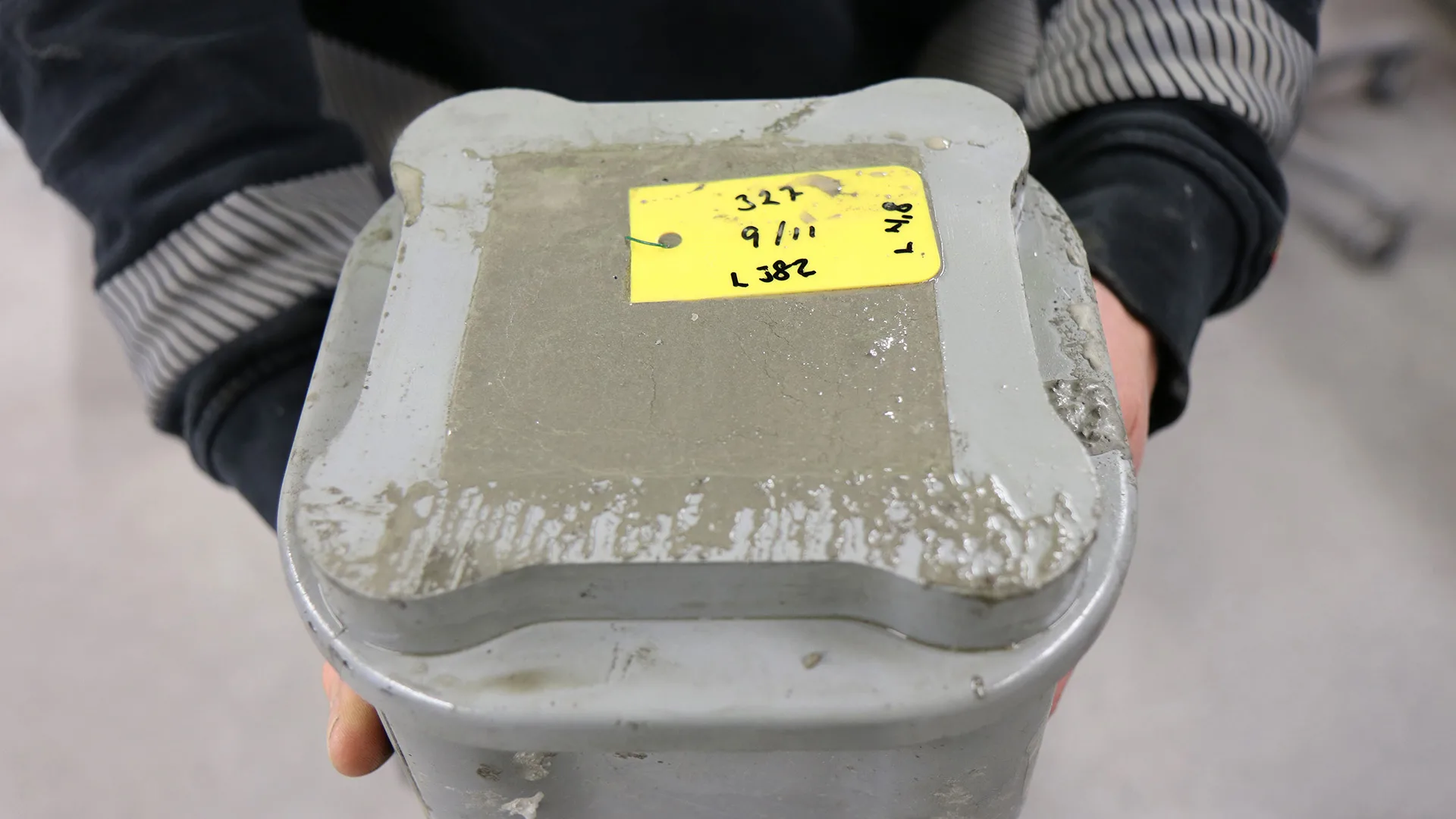
The Kiruna mine reduces carbon dioxide emissions by a staggering 60 tonnes (!) per day. This is made possible by replacing cement with GGBS – a slag product from steel production.
– The concrete industry is a major source of carbon emissions and we are working hard to find other, sustainable and long-term solutions. This is an important part of that work, says Benjamin Krutrök, Group Manager at LKAB Berg & Betong.
Few have missed the Swedish cement crisis, which hit full force in the summer of 2021. There is still no long-term solution in place, and this means that Sweden is at risk of suffering a major shortage of cement. And that has consequences, not least for LKAB, which needs cement to reinforce rock. There is nothing more important than safety underground, which means that rock reinforcement and mining production go hand in hand.
– Europe has been using blast furnace slag in concrete production for a long time. The reason why we have not done so in the past is that the conditions have not been right. It’s also about the requirements we have to meet, says Benjamin Krutrök.
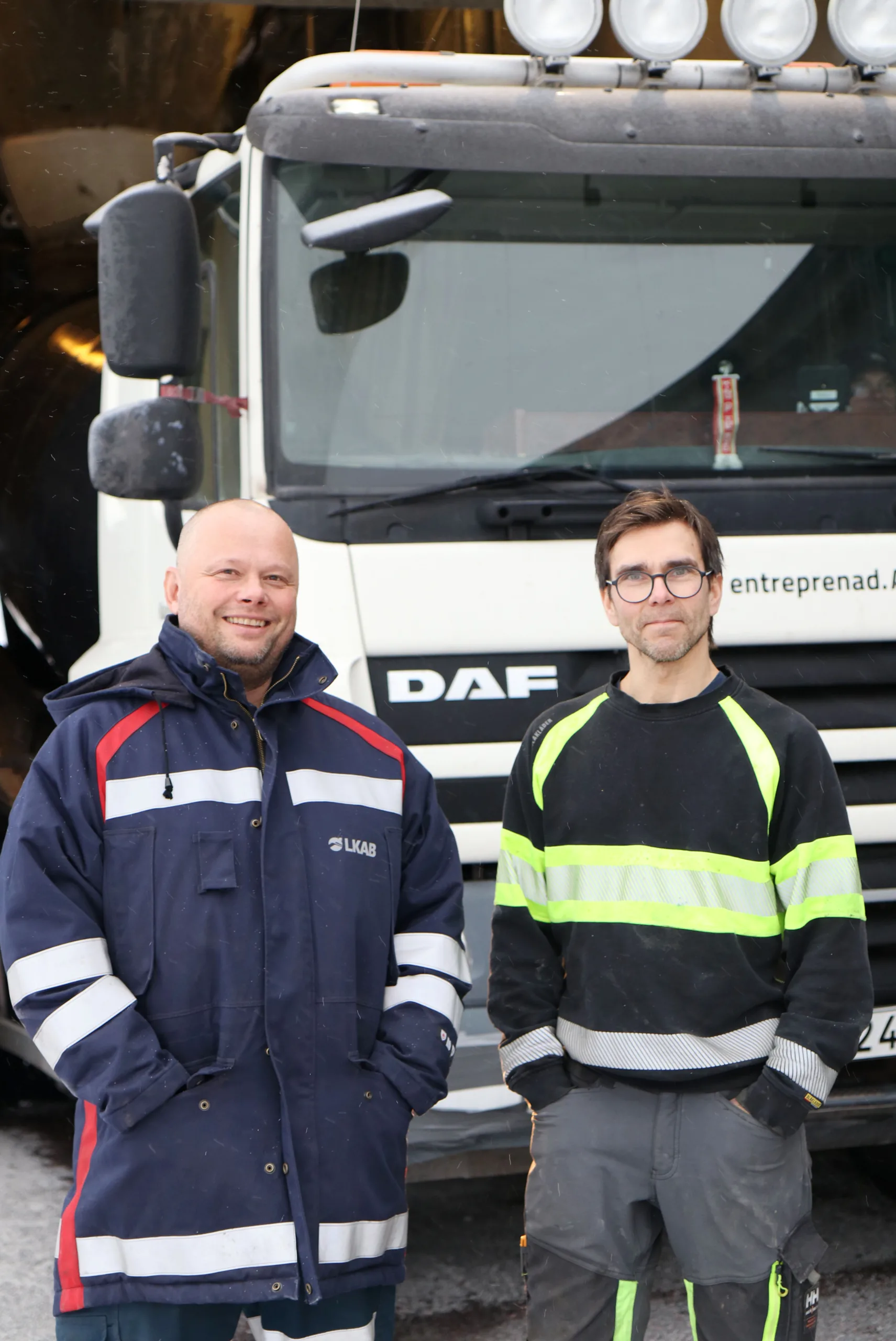
GGBS is thus a residual product from steel production and since September this year there has been a depot on site in Skellefteå. As soon as it went into operation, LKAB Berg & Betong also signed a contract with the supplier.
– According to the requirements we must comply with, we can only replace 30% of the cement with GGBS. But that doesn’t apply to all concrete, says Benjamin Krutrök.
Of the total amount of concrete produced in the concrete plant each year – about 160,000 cubic metres, the so-called excavated concrete is exempt from the requirements that apply to a large part of the infrastructure-adapted concrete.
– We use about 80,000 cubic metres of concrete for shaft renovations every year. When I was asked to test this solution on a larger scale, it felt natural, says Mikael Kyrö, production manager for the shaft group at Kiruna Mine.
The infrastructure and production flow in the mine is largely based on shafts, which are used to transport the ore from the production areas to the main level for crushing and feeding. Unfortunately, the shafts suffer from several problems that require reinforcement measures – shaft concrete.
– We have tried mixing in 50% GGBS and it works well. We will increase that amount further, says Mikael Kyrö.
But using GGBS is not a cheaper solution. It is, however, a much better and more sustainable solution with several added values.
– For me, it is important that our children will be able to ski in the future as well, says Mikael Kyrö and continues.
– Every day we reduce carbon dioxide emissions by about 60 tonnes. LKAB Berg & Betong, one of Sweden’s largest concrete producers, has a clear goal in mind. Operations will be converted to produce fossil-free concrete.
– In the long term, we want to become a carbon dioxide-free supplier, says Benjamin Krutrök.
BRIEF FACTS
- LKAB Berg & Betong’s concrete plant in Kiruna produces around 160,000 cubic metres of concrete per year.
- By replacing part of the cement with blast furnace slag (GGBS), carbon dioxide emissions can be reduced by 60 tonnes per day.
- This means that carbon dioxide emissions can be reduced by about 13 000 tonnes per year.
- Around 80,000 cubic metres of shaft concrete will be produced using GGBS as a base – instead of cement.
- GGBS currently replaces 50 percent of the cement in the shaft concrete used to renovate rock shafts in the Kiruna mine.
- A total of 38 shafts in the Kiruna mine.
- Shaft renovations are carried out in three stages and each stage requires about 12 000 cubic metres of concrete.
- By replacing cement with GGBS, LKAB Berg & Betong reduces carbon dioxide emissions by around 1,700 tonnes every month.
- LKAB Minerals produces over half a million tonnes of GGBS in the UK. This reduces customers’ carbon dioxide emissions by more than 500,000 tonnes.