Developing the mine of the future
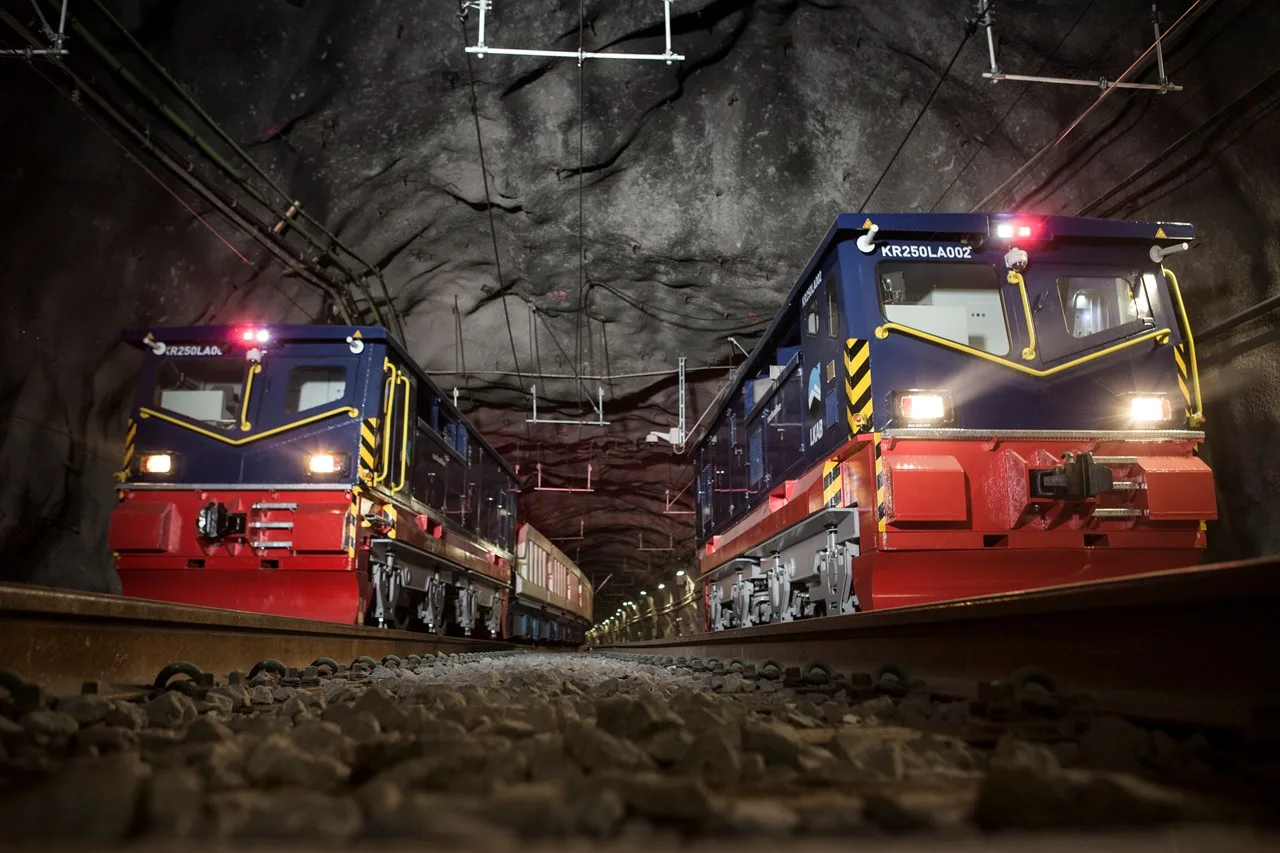
The mine of the future is carbon-dioxide-free, digitalised and autonomous. To realise the technology shift and reduce climate impact, LKAB has joined forces with several Swedish industrial companies to form SUM – Sustainable Underground Mining.
The testbed, SUM, will be created in LKAB’s underground mines in Kiruna and Malmberget and in a virtual mine. In the test facilities technology will be developed and tested in a real mining environment which is the basis for the collaborative project. LKAB is the project owner and will take the lead to drive development.
“Right now, we are in the preparatory stage and are planning for the project, which will be conducted over a period of several years,” says Carlos Quinteiro, mining technology specialist at LKAB.
SUM will develop a basis for designing future mining and production systems.
“If we are to remain a competitively strong company in the future, we have to think in a new direction. We can’t use a copy-and-paste model of previous main levels; i.e., design and build future main levels like we do today. For example, we have to take the greater mining depth and increased rock stresses into consideration. Among other things, this means that we must study alternative mine layouts and placement of ore passes. Quite simply, we have to look at the entire mining process,” says Carlos Quinteiro.
The mine of the future will require new control systems, new and improved mining equipment, as well as efficient management systems that meet future demands for a sustainable industry.
“Eventually, we will phase out fossil vehicle fuels. If we’re going to be a sustainable company, we have to look at other alternatives, such as battery operation and autonomous equipment. To get there we have entered into a strong collaborative venture in which our partners have strengths in their respective areas,” says Carlos Quinteiro.
The time perspective is relatively short and new solutions must be up and running by as early as 2030. In fact, after 2030, LKAB must be ready to mine iron ore at even greater depth. This is contingent upon a decision being taken in the mid-2020s as to how production will proceed under the present main levels.
“We have developed solutions and methods that have been adapted to our specific conditions for a long time. Some things work really well; for example, large-scale sublevel caving. In those cases, it’s a matter of refining and adapting the methods for future use,” says Carlos Quinteiro.
Within the framework for the testbed the best way of building an efficient, autonomous production system that is carbon-dioxide-free and safe will be investigated. People and machines will work side by side in the future autonomous and digitalised mine.
“The future mine will be very different from today’s, but I am convinced that it will be a more sustainable and safer mine. It’s not about phasing out people in favour of machines. Instead, it’s a matter of introducing new types of work and new ways of working,” concludes Carlos Quinteiro.