Why carbon dioxide-free sponge iron?
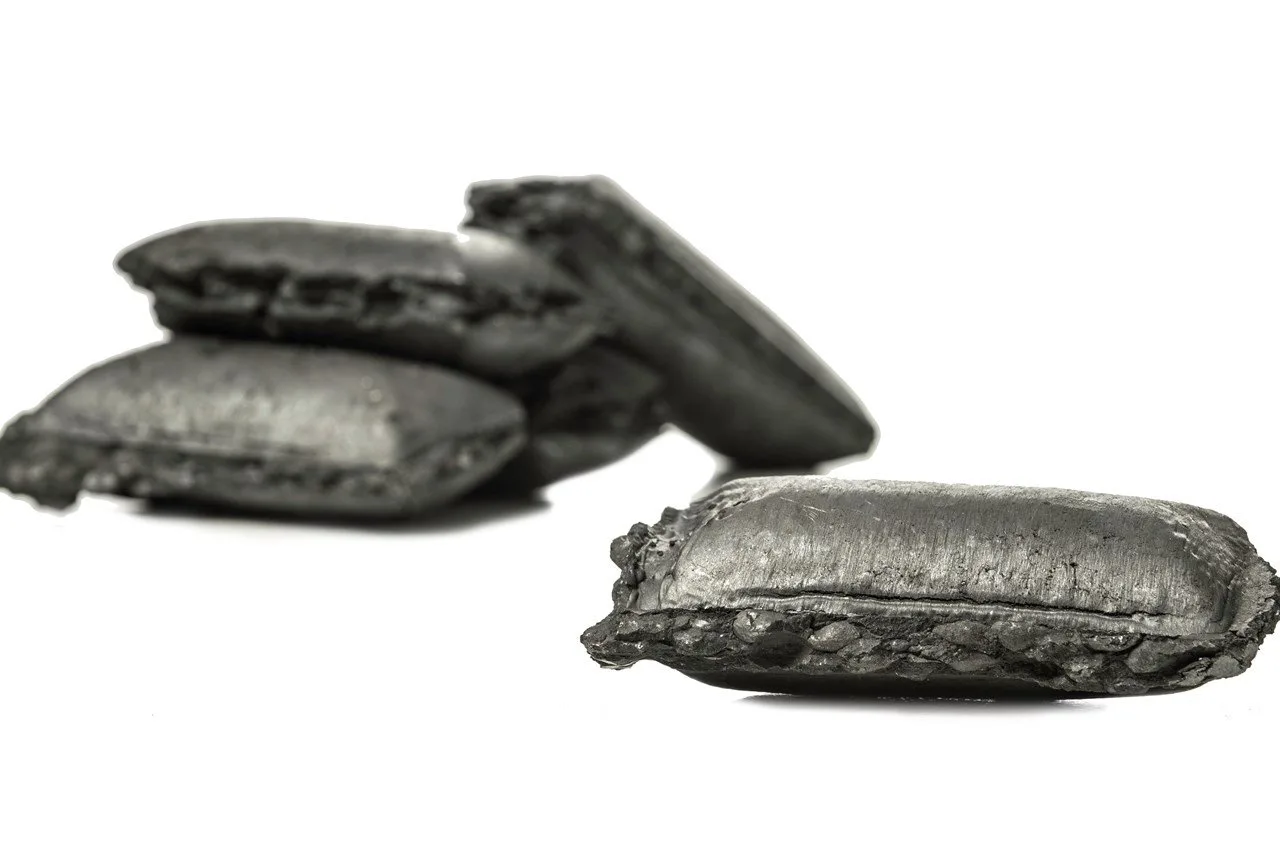
The company's new strategy will entail many changes, one of the more obvious of which is the new product – carbon dioxide-free sponge iron, which will eventually replace conventional iron ore pellets. But why, and what are the differences?
LKAB’s new strategy charts the path towards zero carbon-dioxide emissions from our processes and products by 2045. LKAB’s pellet products are now among the world’s most climate-efficient iron ore pellets. Even so, our operations give rise to large emissions of carbon dioxide. Considerable emissions also arise later in the value chain, when our pellets are processed to make finished steel. By taking this leap forward in the value chain and starting to deliver finished C02-free sponge iron, we can contribute to a reduction in global emissions of about 35 million tonnes of carbon dioxide annually, which corresponds to two-thirds of Sweden’s total emissions. This represents an enormous climate benefit.
What is sponge iron? Sponge iron, or DRI (Direct Reduced Iron), is essentially the next stage in the process chain after iron ore pellets. Unlike pellets, which still contain oxygen and must be further processed by the customers, sponge iron is pure, ready-made iron.
“Today’s iron ore pellets must be reduced to iron before being used in steelmaking. To do this, customers use our pellets either in a blast furnace or in a direst reduction plant for production of sponge iron, often with the help of fossil carbon. Sponge iron is thus already produced in many steel-producing countries, but we are now going make it ourselves with fossil-free energy and without carbon dioxide emissions,” explains Mikael Pettersson, senior project manager, Market and Technology.
At LKAB the sponge iron will be compressed to form so-called HBI (Hot Briquetted Iron). Among other things, the aim is to facilitate transport of the products. So, why is this change being made? There are a couple of main reasons. First, there is the environmental perspective.
“By taking part in this transition we are helping to develop a solution for a problem that we are otherwise contributing to. The steel industry accounts for a large part of the world’s carbon dioxide emissions. Carbon-dioxide-free iron ore products create possibilities for producing carbon-dioxide-free iron and “green” steel. And fossil-free steel will play an important role in the development of a sustainable society, since it will be used in, for example, wind turbines, electric vehicles and other technologies,” says Mikael Pettersson.
In part, it has to with assessing business potential. With the switch to sponge iron, we increase the value of our products and that gives LKAB the prerequisites for more than doubling sales by 2045.
“In a market that places high demands on carbon-dioxide-free production, this secures the company’s business leading forward,” says Mikael Pettersson.
According to forecasts, the market for steel will grow by 50 percent by 2050. It is believed that scrap-based steel produced in electric arc furnaces will account for all of that growth. Unlike sponge iron, conventional iron ore pellets cannot be used in the electric arc furnace.
Undoubtedly, the transition will entail challenges for the company. Development towards the realization of LKAB’s new strategy encompasses the entire value chain from mine to finished product, including all logistical aspects.
“We are making preparations for manufacturing, handling and transporting a new product which places completely different demands on both processing and logistics. It is too soon to say exactly how all of this will take shape, but this will become apparent as development work progresses. This is a major shift, but it is something for which there is great market demand. Here, we see very great opportunities,” concludes Mikael Pettersson.