Mine waste will now be utilised
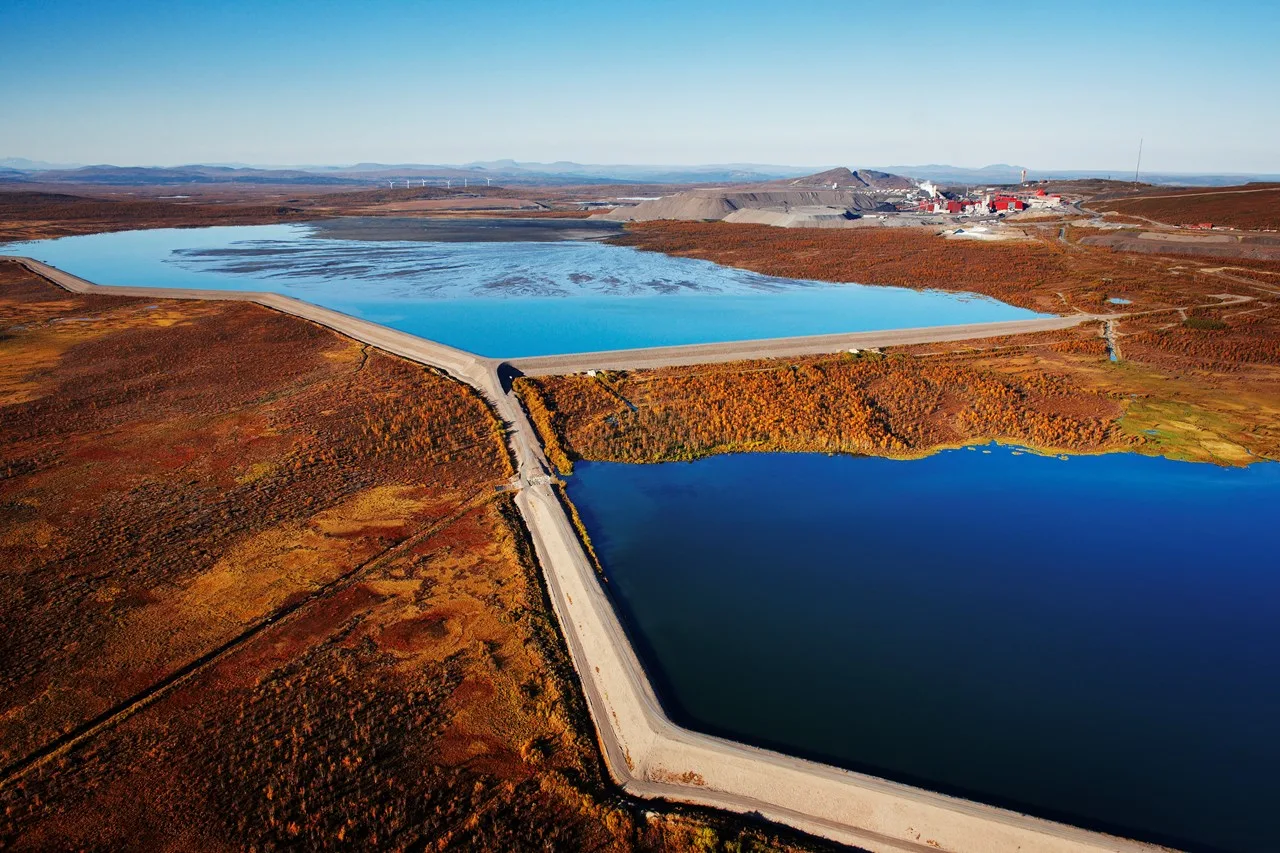
Residual products from LKAB's mines include both phosphate minerals and so-called rare earth metals, materials which up until now have ended up in tailings ponds. It is hoped that these valuable minerals will now be recovered and utilised with the help of innovative new technology.
Apatite is a phosphate mineral that is used in, among other applications, the production of fertilisers and it is in the ore that is mined in LKAB’s mines. Previously these minerals were extracted, but production was mothballed in the mid-1980s. Since then, the apatite has been a part of the the mine waste that has been sent to the tailings ponds. The problem is that it is very difficult to make production of LKAB’s apatite concentrate economically viable. The product must be further upgraded. This is where EasyMining, a subsidiary of environmental services company Ragn-Sells, comes in. They have developed and patented a method for upgrading apatite concentrate to a finished product called MAP, or Mono Ammonium Phosphate.
“LKAB is responsible for the entire project, from raw material to production of apatite concentrate and manufacturing of MAP. The project is being carried out in close collaboration with EasyMining, who are contributing their knowledge of the manufacturing process for MAP,” says Lars Vikström, technical and business development manager at the Special Products Division.In addition to phosphate, the mine waste contains rare earth metals.
“Although there are relatively small amounts, the material is of interest for us. Here, in principle, the challenge is to sort out and separate what is of value,” explains Ulrika Håkansson, technical business developer at the Special Products Division.Rare earth metals, as much as 95 per cent of which are produced in China, are used in, among other products, mobile phones, batteries and magnets. Heavy and light rare earth metals and phosphorus are all on the EU’s Critical Raw Materials list; i.e., materials that are of major future importance for the EU economy, industry, technology and environment and the supply of which cannot be considered stable. The EU is currently wholly dependent on imports of rare earth metals, and a single deposit in Europe meets barely 10 per cent of EU phosphorus demand. Here, there are great opportunities.
“For LKAB, this is an industry in which we are not yet active, but it has the potential to be an additional niche. It is too early to say where this will lead and we are in an early stage of development, but we really believe it is viable,” says Lars Vikström.After initial laboratory trials a pilot facility will now be built to determine if the technology can be taken to industrial scale.
“The pilot plant is a mobile unit that can be operated at the concentrating plant. We will run and test the plant in both Malmberget and Kiruna to assess differences in materials and to verify whether or not it works as it should,” says Ulrika Håkansson.The prestudy will be concluded in 2019 and, by 2020, it is hoped that the technology can be taken to full scale.
“We have two exciting years ahead of us. It’s an ambitious plan, but we are optimistic and we believe it will work,” says Lars Vikström.