Measures for safer and more efficient mining
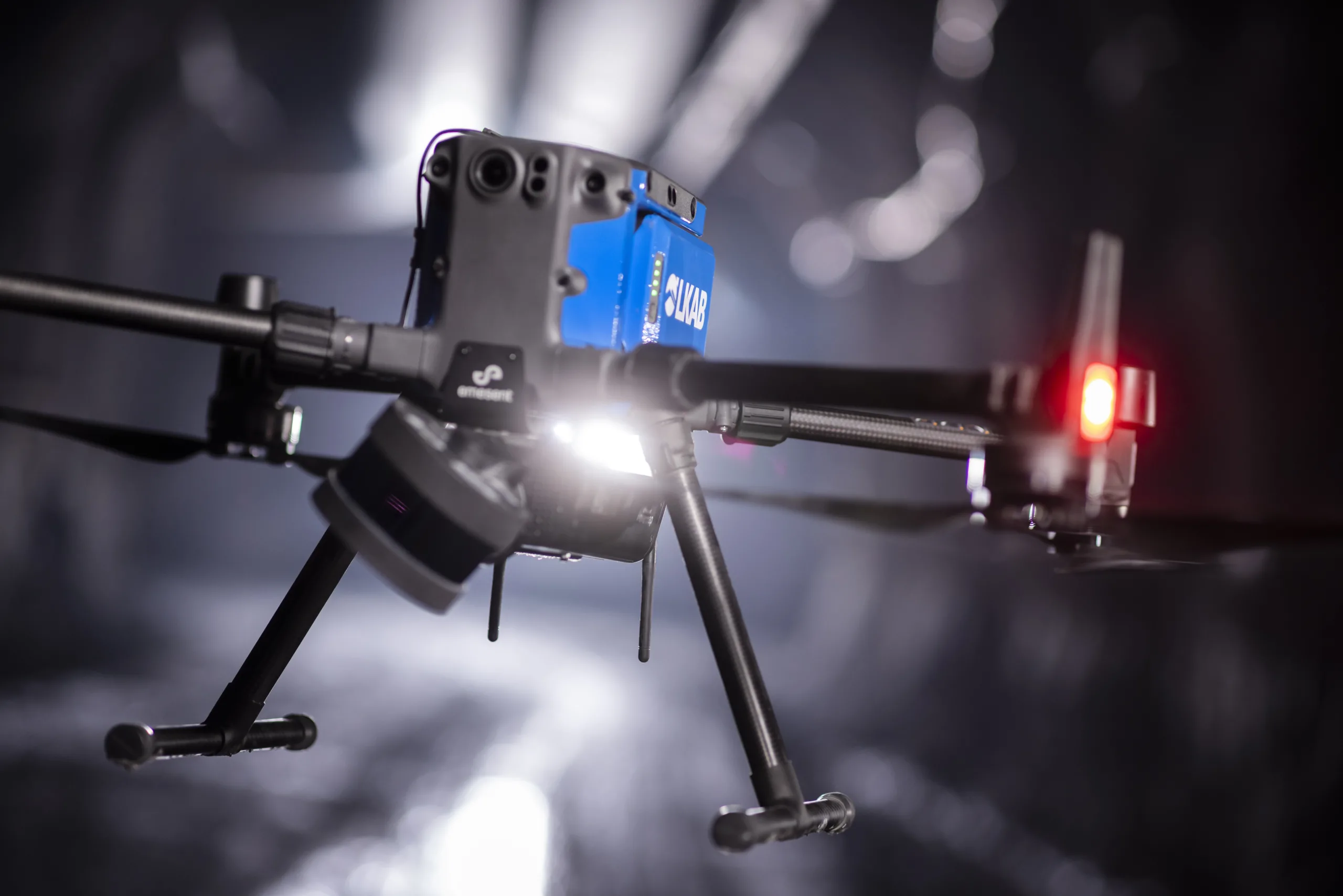
Safety comes first – in every situation. In fact, under ground, nothing is more important. Therefore, we are implementing more initiatives for even safer, more productive mining at greater depth.
Rock stresses increase as mining moves to ever greater depth. They can never be eliminated or reduced. But they can be transferred and controlled, for example, by adapting the mine layout, i.e., how production, infrastructure – roads and production areas – are planned and placed in relation to factors including the geology. When an orebody is mined out, rock stresses must find new paths around and under the mined-out area. This is when rock stress concentrations are induced and, if the stresses exceed the strength of the rock mass, the rock mass ruptures, or cracks. Seismic activity, sudden failures in the rock mass, release enormous amounts of energy.
“When we mine at greater depth, we have to deal with higher stress concentrations. Therefore, it also becomes more important to plan production based on the rock mechanical conditions,” says Anders Wälitalo, group manager for rock safety at LKAB in Kiruna.
In other words: mining must be guided by the properties, conditions and stability of the rock mass, because the rock mass dictates the prerequisites for production.
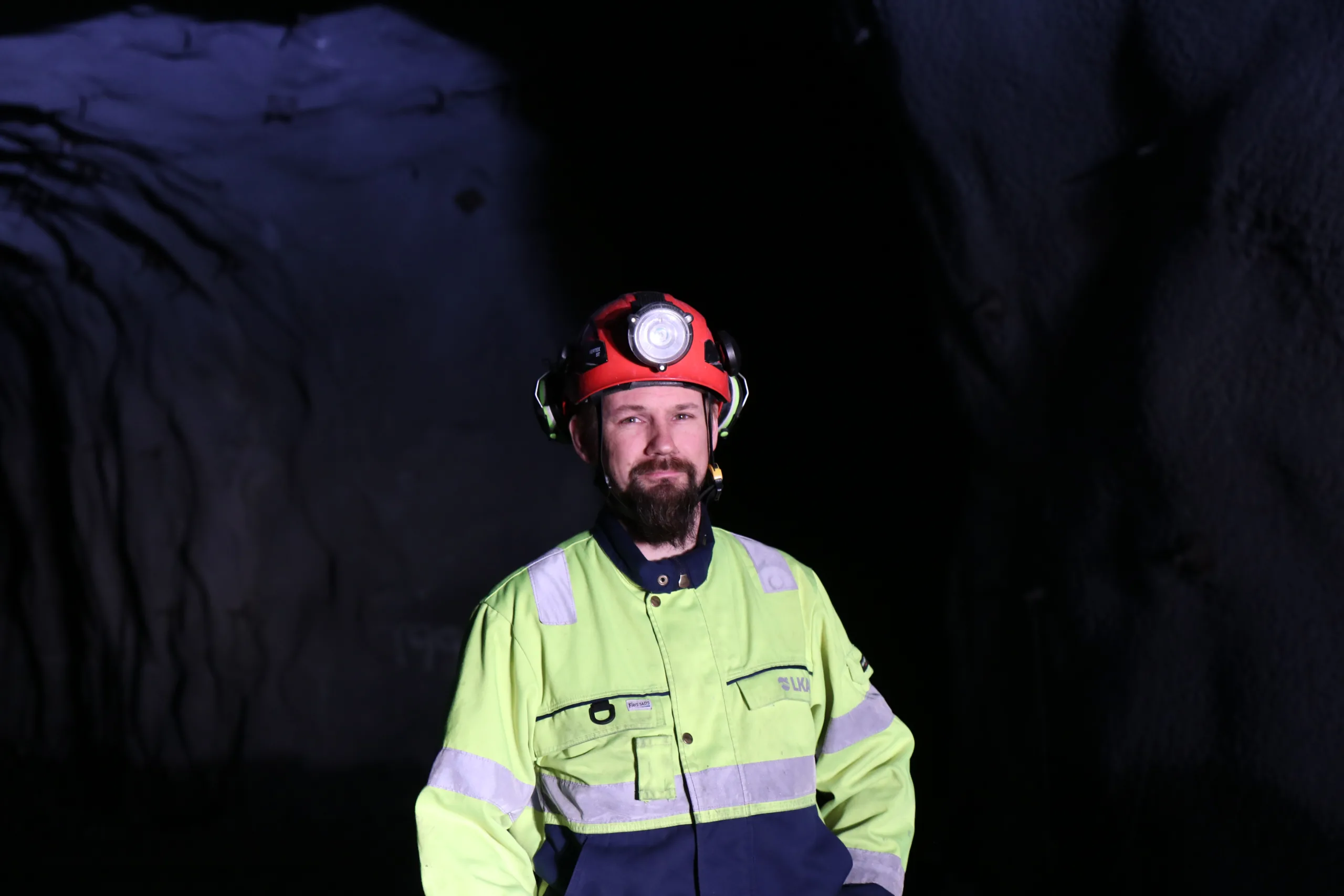
Energy is stored in the rock mass
To control, predict and sometimes even activate seismic events in specific areas is complex. But necessary and a priority. This is all about safety and placing high demands on proactive, preventative work, where several parameters must be taken into consideration.
“We are working on a broad front, based on a holistic approach, which means that we have to look at all activities, how they interact and how they affect each other. Everything is interdependent and nothing happens autonomously or without causing some kind of impact in the mine. Quite simply, how we choose to plan, design and proceed with the mining operation is crucial,” says Christina Dahnér, seismology specialist at LKAB in Kiruna.
As the saying goes, no chain is stronger than its weakest link; everything is interconnected in one way or another. This makes mining a particularly complex operation.With every change in production volume and every metre driven, the game rules change and a new starting point presents itself. It all has to do with how the chosen mining method affects the rock mass. That method largely dictates the framework for production. Therefore, in a mining context, operators must know the method inside-out in order to be able to predict the impact of mining.
“We work with several activities to minimise larger seismic events in the footwall. Above all, we do this by keeping a close eye on sequencing; that is, how the mine is mined out, in what order and how mining proceeds successively at depth,” says Christina Dahnér.
Hanging wall and footwall
Let’s start with large-scale sublevel caving – the mining method used in LKAB’s underground mines. The method gives rise to mining-induced subsidence, which means that the rock mass on the hanging wall is blocked up, fragmented and successively caved in to the mined-out areas, but in a highly controlled manner. In a sublevel-caving context there is always a hanging wall and a footwall on either side of the orebody (or orebodies, if several separate orebodies are being mined). In the case of the Kiruna mine the hanging wall lies in the direction of city and on the footwall side we have the mine infrastructure, roads and mine shafts.
“When ore is mined out, there is no longer support for the hanging wall. This means that the hanging wall expands towards the area in which ore has been mined out,” explains Anders Wälitalo.
But mining also affects the footwall, in two ways, due to stresses and displacements.
The stresses must find a new path as mining proceeds, under the area that has not yet been mined, which results in a higher stress concentration in the footwall.
“Seismic events in the hanging wall, where there are no personnel or infrastructure, are preferable to events occurring in the footwall. The more we can reduce seismic impact in the footwall, the better,” says Anders Wälitalo.
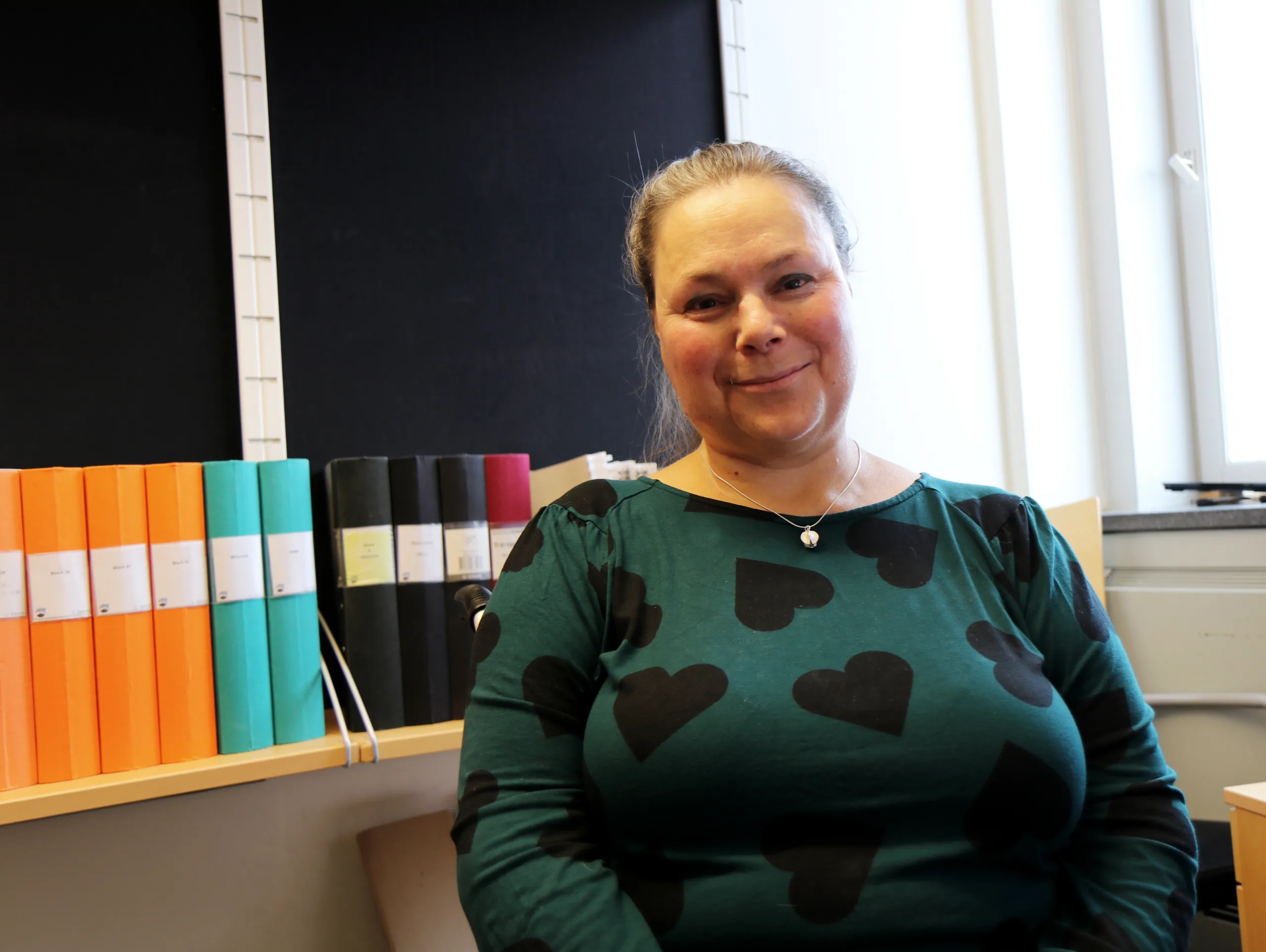
But mining also affects the hanging wall. And so it should, in order to ensure safe and efficient production. An important factor is the degree to which the hanging wall subsides and successively caves in to the voids that are created as the orebody is mined out. In the case of the Kiruna mine, since the orebody is both long and wide – but not uniformly wide across the entire body – a considerable amount of waste rock, or barren rock, must be removed to ensure optimal flow and balance. Therefore, measures are taken to activate the hanging wall, since a ‘silent’ hanging wall may indicate that the rock mass bears large stress loads. This, in turn, increases the risk of major seismic events.
“The deeper we mine, the greater are the challenges. Planning the rate at which mining proceeds at depth is therefore decisive. How we choose to mine the orebody is crucial for safety and efficiency,” says Anders Wälitalo.
Seismic events in the hanging wall
How the mine is successively mined out has a bearing not only on production and volumes. This also has a bearing on the seismic events, of which there are several hundred – every day. Most of these events are, however, so small that they can only be registered by very sensitive instruments, but they are sometimes large enough that they can be perceived by local residents, especially if they occur in the hanging wall, which is situated closer to the urban area.
“In the case of events in the hanging wall, vibrations are often noticeable. This does not necessarily mean that the magnitude of the event is particularly great. If the event occurs relatively close to the surface, the vibrations are more noticeable that they would be if the event were deeper down in the hanging wall,” says Christina Dahnér.
In a mining context there is seldom a single answer to a question. This is because, most often, several factors weigh into the equation.
“Due to changed sequencing – to ensure safety under ground – changes in the behaviour of the hanging wall can arise. This is now being investigated,” says Christina Dahnér.
The revised sequencing is due primarily to the need to control events in the hanging wall, far from personnel and infrastructure. But the increased vibrations are also explained by the fact that mining is taking place closer to settlement areas that have been, or are being, phased out. Last but not least, the major seismic event which occurred in May 2020 continues to have an impact on mine production and ground deformation.
“We have deduced that a smaller seismic event in the mine triggered the Block 22 event. That gave rise to larger movements in the rock mass, in the hanging wall. At surface level a vertical movement of about three centimetres was recorded and the sudden subsidence in the rock mass generated the energy that was released when the event occurred,” explains Joel Kangas, mine manager at LKAB in Kiruna.
The underlying cause of the large movement in the rock mass was that the hanging wall had not been blocked up in the right way. In light of this, it was decided that a stable, load-bearing pillar would be left in the Block 22 area, which means that the mine effectively becomes two mines.
“This is the safest alternative for safeguarding against movements in the hanging wall at a later date and for reducing seismic events. That last thing we want to do is trigger a similar event,” says Joel Kangas.
The mining organisation is working proactively to minimise the vibrations that reach the surrounding settlement area through efforts to reduce the magnitude of major seismic events. This is done, for example, by adapting production blasting.
“I understand that many people feel anxious and have concerns that more seismic events are taking place in the mine, and that there may be rockbursts or potential hazards. I wish to reassure local residents that there is no imminent danger, because we are doing all we can and more to ensure that the mine is as safe as possible,” says Joel Kangas.
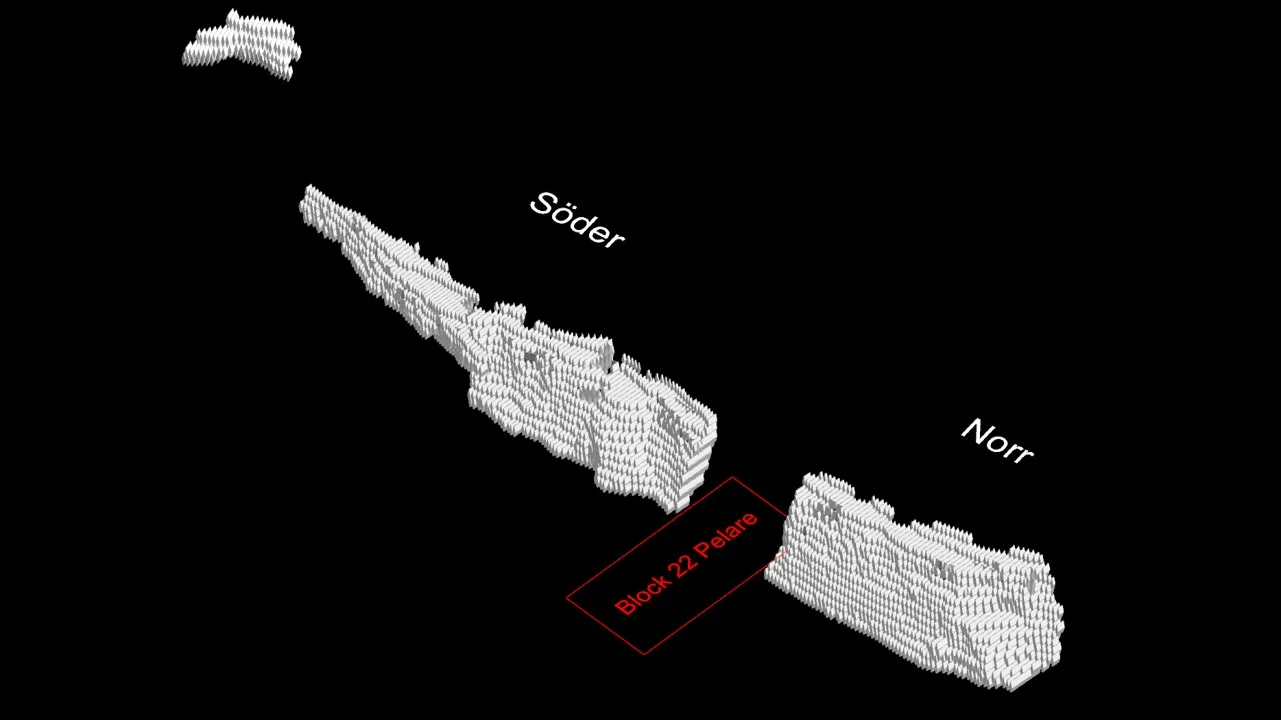
One mine becomes two
The change entailed by the pillar for the Kiruna mine will not actually be realised for some time. Initially, the task will be to revise much of the original plan, adapt mining and successively increase production based on the condition of the rock mass.
“The pillar solution gives us a bit more flexibility, since the southern mine will not be impacted by operations in the northern mine, and vice versa. On the other hand, production must adhere to a pattern, since the production areas are interconnected,” explains Joel Kangas.
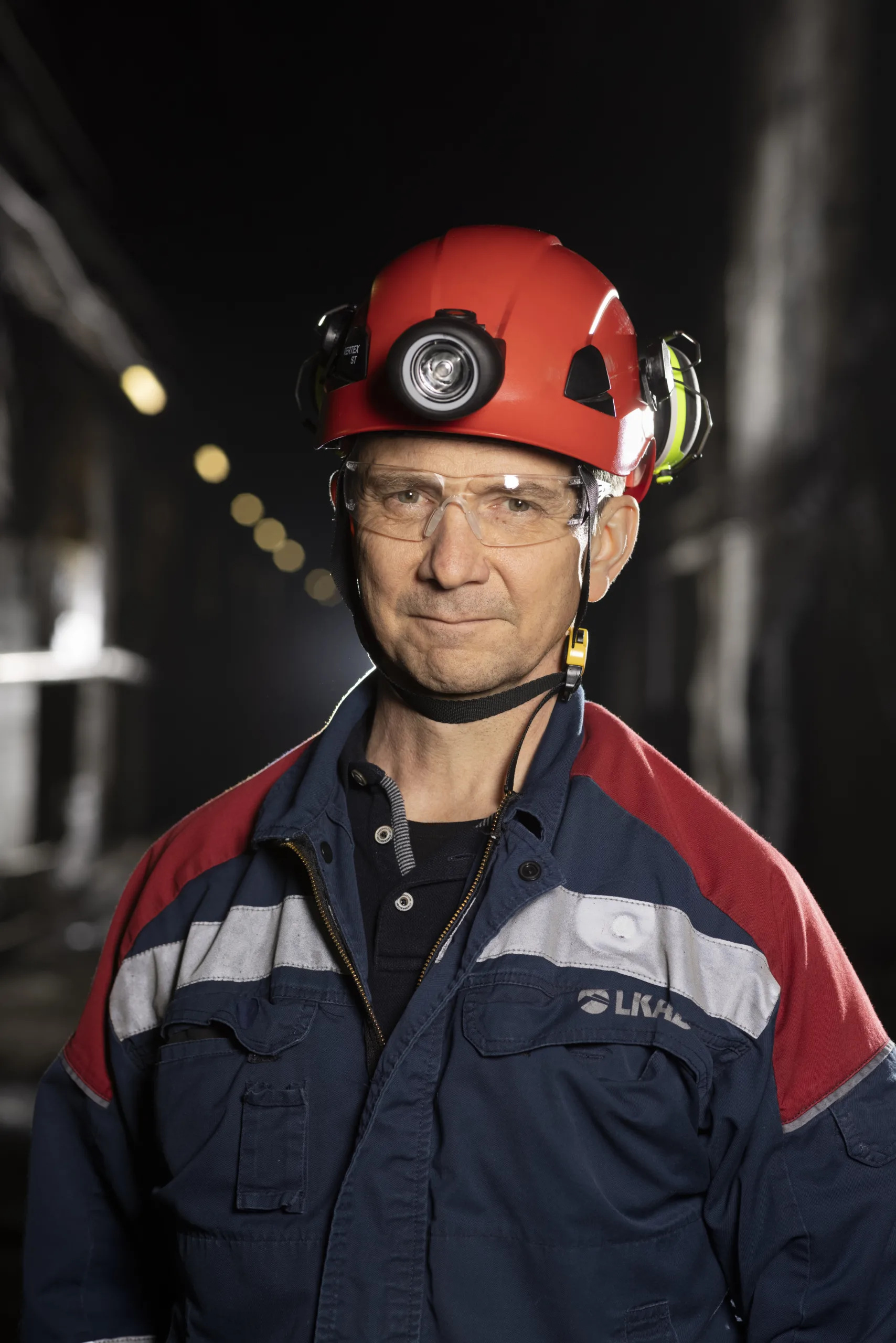
The perceived feeling that a seismic event is occurring is not synonymous with an event in the mine’s footwall, in the production areas where personnel and machines are at work. Nor is it synonymous with danger or rockbursts, and it is most often due to events in the hanging wall, far away from the footwall.
“During 2022 six events in the hanging wall with a magnitude exceeding 1.5 were registered, according to the local scale. During 2023, 23 events have occurred in the hanging wall,” says Christina Dahnér.
The increase in events in the hanging wall is expected and is a consequence of measures taken to reduce events in the production areas. In other words, this ensures an even safer mine at greater depth.
“After the major event in 2020 we became even more aware of the importance of an active hanging wall. Therefore, we have also been working to implement several changes. In a way, you could say that we have turned the situation around, from the footwall to the hanging wall,” notes Christina Dahnér.
Thus, more events occur in the hanging wall than previously, while fewer events take place near the mine infrastructure, in the production areas and close to where people are present.
“Again, I fully understand that many people experience discomfort when events occur, but I hope that we have succeeded in clarifying what seismic events are and that they can take place in either the hanging wall or the footwall. Seismic events will occur as a natural consequence of mining-induced stress redistribution. But we are working to minimise the magnitude and control where they occur,” says Joel Kangas.
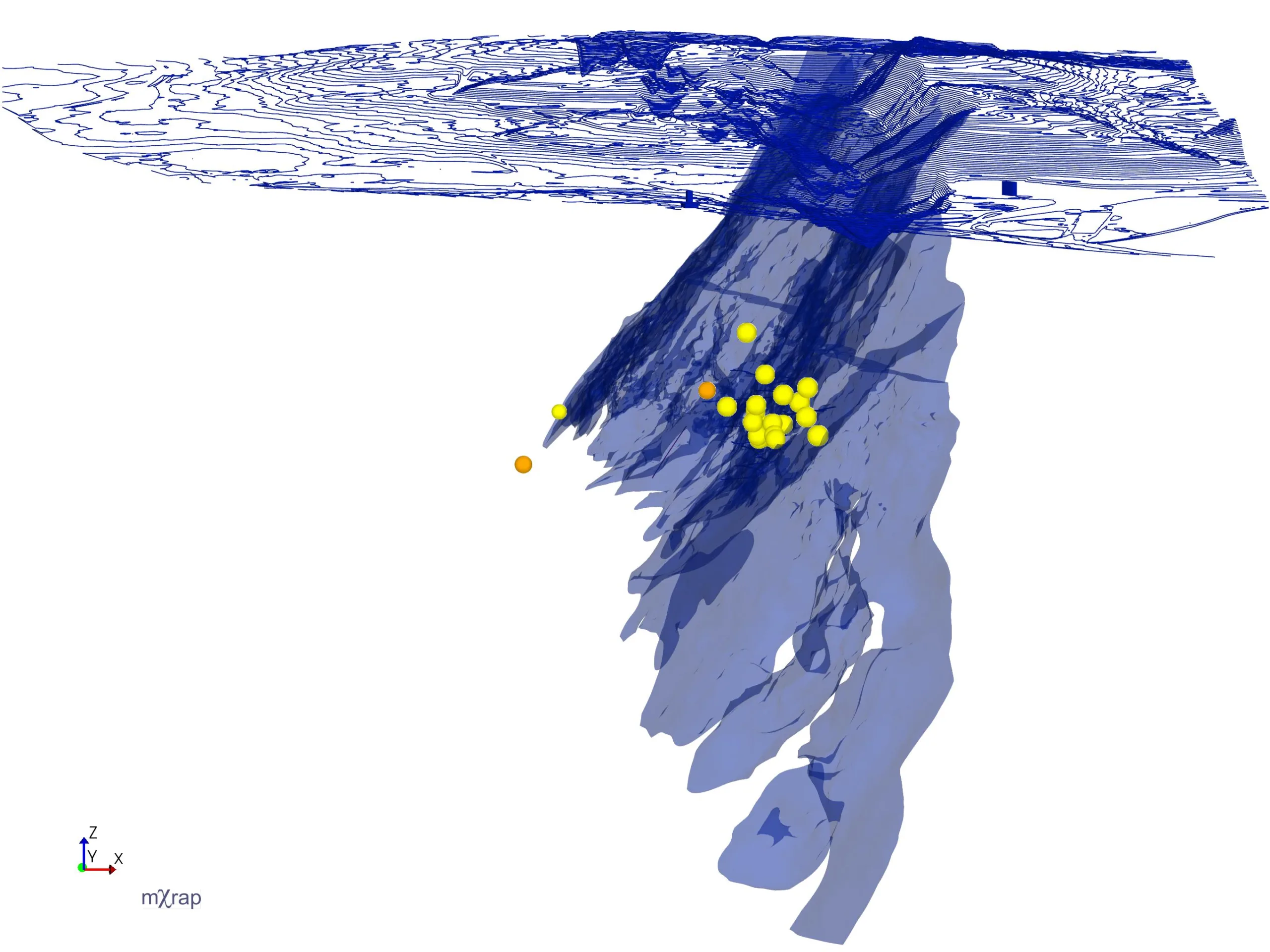
Text: Josefine Ejemalm