Developing the processing plant of the future
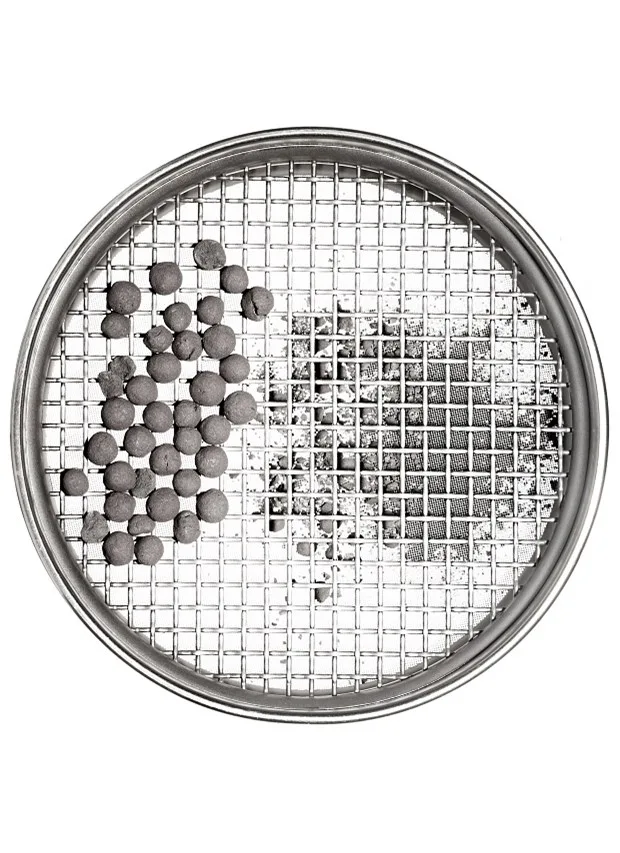
The next-generation pelletizing plant is starting to take shape. So far, only a few pieces of the puzzle are in place, but they represent several major steps towards the realization of LKAB's new strategy.
“Right now we’re looking for the best way to utilize oxygen, which is a residual product from the HYBRIT process, in our pelletizing process,” says Tiago Ramos Ribeiro, research engineer at LKAB in Malmberget.
As LKAB leads the transformation of the mining industry into a sustainable future, we also seek to totally eliminate emissions of carbon dioxide from our processes and products. The new strategy will be realized by 2045, so the transition must be made relatively quickly. And this transition is revolutionary.
“Within our development programme to create the next-generation pelletizing plant, we are working with oxygen as an enabler for energy-efficient, climate-impact-neutral products,” says Björn Åström, project manager at LKAB in Kiruna.
But, as the saying goes, Rome wasn’t built in a day. The same can be said of the pelletizing plant of the future. Instead, this will entail a gradual shift, where oxygen plays a part in one of the first major steps towards the conversion of present-day technology.
“We’re working with the next-generation pelletizing plants in three phases; with the current process, the modified process and the future process,” explains Björn Åström.
If LKAB is to be part of the solution, instead of being part of the problem, the conventional, climate-harmful fossil fuels used in mineral processing – coal and oil – must be replaced. Oxygen will thus be a part of the solution, since it will be a residual product from the HYBRIT process, which is based on hydrogen technology. And it is carbon-dioxide-free.
“We have the potential to reduce carbon dioxide emissions and fuel consumption by utilizing oxygen while at the same time increasing productivity and improving product quality,” says Tiago Ramos Ribeiro.
LKAB’s Malmberget operation will be the first to make the transition, which means that a demonstrator reduction shaft furnace must be built, and that will require a huge volume of hydrogen gas. This also means that the pelletizing plants in the same location will be first up for the generation shift.
When lab testing and modelling have advanced further along this route, the next step, refitting of the existing pelletizing plants, will take time. Already by 2025, the working group will submit proposals on the design and construction of the plants. Production will be up and running during the following year.
“There is great potential for building the reduction shaft furnaces close to the pelletizing plants; we can save energy by avoiding pellet-cooling prior to reduction and we can optimize the product, since all pellets will be reduced. We want to allow the pellets to heat successively before charging them hot into the reduction shaft. One issue we need to resolve is how much we need to oxidize and sinter the pellets,” says Björn Åström.
However, there are already several exciting and promising results to build on, even though many questions remain unanswered and many stones must be turned.”We have to determine how oxygen can be used in pelletizing; where, how much and in the most efficient way,” explains Tiago Ramos Ribeiro.
In other words, it is still too early to say with any certainty what the future has in store.
“In our pilot-scale tests, among other things, we have seen minor variations in the pellets. They show generally high and consistent quality. We have also succeeded in heating up the pellet bed faster and with less energy,” says Tiago Ramos Ribeiro.
The work now being done in this development programme is partly funded by Swedish Mining Innovation and is being conducted in collaboration with Luleå University of Technology, Kaunis Iron and Metso Outotec. Therefore, much of the work can be described as basic research.
“We’re looking at individual pellets as well as doing larger-scale tests. Luleå University of Technology will mainly conduct small-scale testing, while we at LKAB are focussing on larger tests, at a level of about 100 kilograms of pellets. This will lay the foundation for the knowledge we need in order to scale up to a fully industrial-scale process,” says Tiago Ramos Ribeiro, continuing,” We hope to be able to achieve a faster and more complete pellet oxidation.”
To complicate the matter, LKAB has two different types of pelletizing plants. One fires the pellets successively on a bed, while in the other, which is a type of rotary kiln, the greatest amount of heat is introduced into the kiln. This means that the so-called straight-grate plant, which is in Malmberget, will be much easier to deal with from the start.
“Oxygen is tougher on our infrastructure and the material in the plant. This is a pressing issue for the future and it has a lot to do with safety,” says Björn Åström.