A carbon free upgrading process starting to take shape
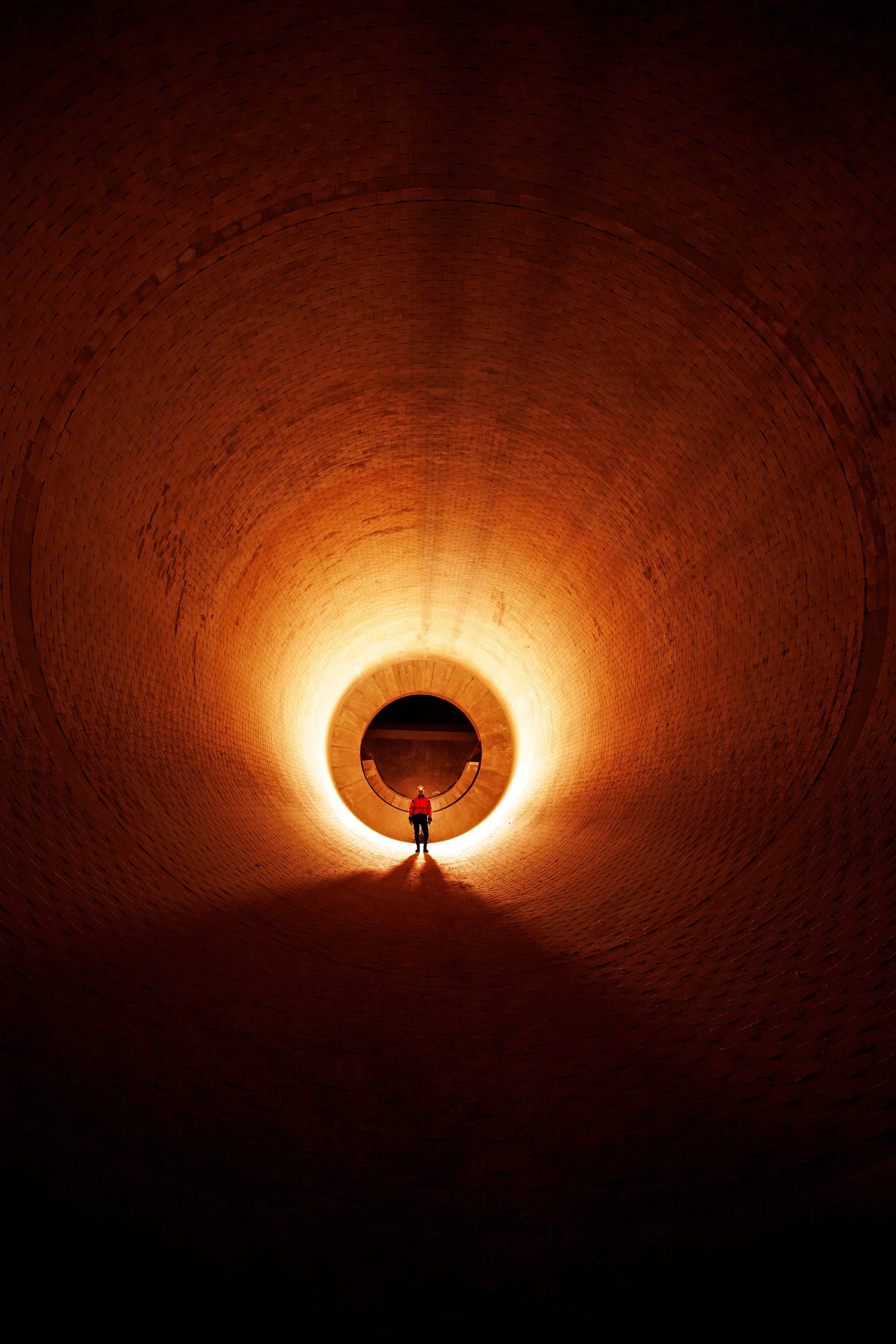
The next-generation pelletizing plant is under development. And, as fossil fuels are phased out in favour of carbon free solutions, co-firing is the most promising alternative. This is the first stage of a multi-stage rocket heading straight into the future. “Our ambition is to replace ten percent of the carbon input with hydrogen by 2026,” says Fredrik Normann, project manager at LKAB.
As LKAB leads the transformation of the mining industry into a sustainable future, this will mean zero carbon dioxide emissions, from mine to port. An extensive mining, processing, and transport process will undergo a radical transformation that requires innovative new solutions.
“Heating in the pelletizing plants is the major source of carbon dioxide emissions in the process. Addressing the heating issue, above all in the grate-kiln plants, is a challenge,” says Björn Åström, project manager at LKAB.
LKAB’s pellet processing operations comprise six pelletizing plants. Four of these, in Kiruna and Svappavaara, are grate-kiln plants. The latter differ from so-called straight-grate plants, in that they are fired under rotation. In other words, in a straight-grate plant the pellets are sintered gradually on a travelling bed, while in a grate-kiln the green pellets are sintered in a large, rotating drum. The greatest amount of heat is introduced into the kiln via combustion of coal and oil.
“In the case of kiln plants we have to consider a very great degree of flaming and heat transfer to the product. That also makes the need for new process technology a much more difficult problem to solve and we have to develop the solution ourselves,” says Fredrik Normann, continuing, “It isn’t a question of a total solution, but a step-wise transition. By 2030, 25 percent of the carbon input will be replaced by hydrogen.”
Carbon free steel
LKAB’s transition has a relatively short deadline. By 2045, the entire operation will have undergone a transformation. The conventional, climate-harmful fossil fuels used in mineral processing – coal and oil – will be replaced. The solution lies partly in the use of biomass and oxygen, but mainly hydrogen. Of the grate-kiln plants, the first to make the shift is KK2 in Kiruna.
“KK2 will be our testbed. This plant is suitably equipped for development and has the lowest production, which makes it ideal for initial testing,” explains Fredrik Normann.
However, LKAB’s pellet operation in Malmberget will be the first to convert. With a so-called straight-grate plant, transition to the new technology will be much easier to deal with.
“No one, anywhere in the world, is doing what we are about to do. This means that we have to be at the forefront of development, which is why we are collaborating with several partners. These include Luleå University of Technology and Chalmers University of Technology, but we are also initiating closer collaboration with one of our suppliers, Metso Outotec,” says Björn Åström.
Pilot trials in 2023
In LKAB’s pilot plant, the so-called ECF, trials will be conducted in late autumn of 2023. This is a crucial step in preparation for large-scale testing in KK2 and it will be decisive for future operations in the carbon free transition.
“There is nothing to suggest that we cannot succeed. It all has to do with developing the technology, and learning more about hydrogen and how emissions arise,” says Fredrik Normann.
But there are also challenges. The phase-out of fossil fuel implies a technology shift which presents many opportunities, but also many questions. Co-firing of hydrogen and the carbon component has never been done in full scale, and hydrogen as the sole source of energy has never been tested in such a large scale. One of many issues that must be addressed is how to ensure that production can continue while the transition is being made, since the heating conditions have a direct impact on product quality.
“We have to make certain that we are getting enough heat to the product at precisely the right time and in the right place while still meeting environmental requirements,” says Fredrik Normann.
In simple terms, the heating issue can be described as a comparison between solid fuel and liquid fuel and how they perform differently in the kiln. Liquid fuel combusts faster and with greater intensity, which is key to solving the heating issue.
“If we fuel with coal, for example, it will end up farther inside the kiln, which means that the energy will be released farther in. On the other hand, liquid or gaseous fuels do not reach as far in, which affects the product quality,” explains Björn Åström.
Safety always comes first
To be able to replace coal with hydrogen a so-called electrolyser will have to be built adjacent to KK2. The project group is looking at the possibility of establishing a plant with capacity for about 20 megawatts of hydrogen, which is the equivalent of about fifty percent of the heating requirement for the pellet plant.
“Learning to handle hydrogen properly and safety has to take priority. This is extremely important and it is a very big part of the whole endeavour,” says Björn Åström.
When hydrogen is used as an energy source in the processing plant, it will be delivered directly from the electrolyser to the furnace in the plant via specially adapted pipelines.
“Hydrogen is a highly combustible gas and, if it is improperly handled, there is a great risk of explosion. The choice of materials is particularly important, since the gas can easily escape, for example, from sealed junctions in the system,” says Fredrik Normann.
Hydrogen gas is reactive, which means that it is flammable, and this places especially high demands on safety. Infrastructure is therefore being designed and built to minimise hazards; for example, the pipeline will be double-layered. In addition, an extensive system of sensors must be installed to monitor pressure changes and fluctuations; safety features in the form of explosion barriers will be installed, and the placement of ventilation systems must be optimised.
“Hydrogen gas involves considerably less handling than solid fuels such as coal. No manual handling is necessary,” says Fredrik Normann.
Power supply is a key concern when it comes to realising a carbon free future. This issue will become even more pressing as hydrogen production is ramped up. In the final analysis, electricity demand will exceed LKAB’s current power requirement by about 1000 gigawatt hours.
“This means that consumption will increase from about 1500 gigawatt hours of electricity to about 2500 gigawatt hours when the Kiruna pelletizing plants are fully carbon free. We have to design a completely new energy system in which hydrogen is produced and stored when we have access to electricity,” adds Björn Åström.
Text: Josefine Ejemalm
- By 2030 carbon dioxide emissions from LKAB’s processing plants will have been reduced by 25 percent.
- This reduction is based on emissions figures from 2020.
- Conversion of the grate-kiln plants will start with introduction of hydrogen in plant KK2.